Bridge Load Test
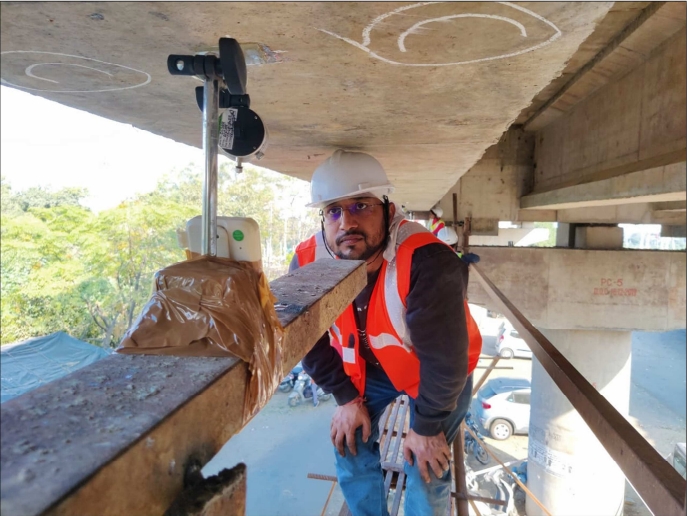
Bridge load test
- Introduction
Bridges are critical infrastructure elements that support transportation networks, often enduring high loads and harsh environmental conditions over extended periods. Regular assessments are required to ensure that these structures continue to function safely and efficiently. Bridge load testing is one of the most effective ways to evaluate a bridge’s performance under load, ensuring its structural integrity.
This detailed report delves into the principles of bridge load testing, focusing on dial gauges and total stations as integral tools for measuring displacement, deflection, and structural response during testing. These tools allow engineers to gather precise data regarding the behavior of a bridge under various loading conditions, enabling informed decisions on rehabilitation or continued use.
- Purpose of Bridge Load Testing
The principal goal of load testing is to confirm that a bridge can safely handle the traffic, loads, and forces it is expected to carry throughout its service life. The specific objectives of conducting bridge load testing include:
- Confirming Load-Bearing Capacity: Ensuring the bridge can bear the maximum expected loads, including traffic, heavy vehicles, environmental forces (wind, snow, etc.), and natural disasters.
- Identifying Structural Weaknesses: Assessing specific areas of the bridge where structural weaknesses or defects may be present, such as cracks, corrosion, or stress accumulation.
- Validating Structural Models: Testing helps validate computational models and theoretical assumptions, which may not always reflect real-world conditions accurately.
- Monitoring Performance Over Time: Over the life span of a bridge, periodic load testing can help track its performance under load, ensuring that it remains functional and safe.
- Informing Maintenance and Rehabilitation Plans: Based on testing results, engineers can develop targeted maintenance or rehabilitation plans to extend the bridge’s life and prevent failure.
- Tools and Methodology in Bridge Load Testing
In bridge load testing, the tools and methodology employed are critical for accurate measurement and evaluation. Commonly used tools include dial gauges, total stations, load cells, strain gauges, and displacement transducers. The following sections provide a more comprehensive understanding of how dial gauges and total stations are used to assess the bridge’s behavior during testing.
4. Dial Gauge Testing in Bridge Load Testing
4.1. Dial Gauge Overview
A dial gauge (or dial indicator) is a precision measuring instrument used to measure small displacements, deflections, or dimensional changes. The primary function of a dial gauge during bridge load testing is to measure how much the bridge structure moves (deflects) when subjected to loads.
Components of Dial Gauges:
- Dial Face: Displays the scale in millimeters or micrometers. The dial face is graduated in fine increments that allow measurement of tiny displacements.
- Measuring Stem: The probe or stem comes into contact with the surface of the bridge to measure displacement. The stem moves vertically or horizontally depending on the direction of the applied force.
- Needle: The needle on the dial rotates in response to the movement of the stem, pointing to the precise deflection value on the dial scale.
The dial gauge can provide real-time readings and is highly accurate, typically in the range of 0.01 mm to 0.1 mm, making it invaluable for identifying small changes in the bridge structure.
4.2. Setting Up Dial Gauges
Selection of Measurement Points
The placement of the dial gauge is a critical step in ensuring accurate measurements. Typically, dial gauges are positioned at specific locations where deflection is expected to be most pronounced. These locations include:
- Mid-span of beams or decks: This is usually the point of maximum deflection for bridges subjected to loading.
- Bridge supports or piers: Measuring deflection near the support points can help assess how the load is distributed.
- Expansion joints or other critical areas: These locations are important for measuring structural movements due to temperature changes or load-induced stress.
Mounting the Dial Gauge
To ensure precise and stable readings:
- The dial gauge should be mounted securely on a rigid surface or bracket.
- The stem should be in contact with the bridge surface but without exerting any pressure.
- The dial gauge should be adjusted to read zerobefore the load is applied to create a baseline measurement.
4.3. Measurement of Displacement
During the load testing phase, the dial gauge continuously measures the deflection of the bridge structure as test loads (usually in the form of trucks or test weights) are applied. The deflection recorded by the dial gauge gives an indication of how the bridge behaves under load, and how much it bends or shifts from its original position.
Static Load Testing:
Dial gauges are particularly useful for static load testing, where a constant load is applied to the bridge, and deflection measurements are taken at regular intervals to observe the structure’s response.
Dynamic Load Testing:
Although dynamic load testing generally requires more sophisticated instrumentation, dial gauges can still provide useful data when measuring vibrational deflections or settling effects in response to moving loads.
4.4. Benefits of Dial Gauge Testing
- High Precision: Dial gauges can measure minute deflections down to 01 mm, making them perfect for detecting small changes in structural behavior.
- Ease of Use: Dial gauges are simple to operate, with no need for complex setup or software. Readings can be taken directly from the dial.
- Cost-Effective: Compared to more sophisticated instruments, dial gauges are relatively inexpensive and accessible.
- Real-Time Monitoring: Engineers can continuously observe deflections and adjust testing conditions immediately as data is gathered.
4.5. Limitations of Dial Gauge Testing
- Point-Specific Measurement: Dial gauges measure deflection at specific points only. To get a comprehensive understanding of the entire bridge’s behavior, multiple gauges are needed.
- Physical Contact: Since the dial gauge measures deflection by direct contact, it may not be suitable for all bridge types or areas where access is difficult.
5. Total Station Testing in Bridge Load Testing
A total station is a sophisticated instrument used for surveying, measuring distances, angles, and displacements with high accuracy. It combines an electronic theodolite (for angle measurement) and an electronic distance meter (for distance measurement) and is used in bridge load testing to monitor and record the structural movements in three dimensions.
5.1. Total Station Functionality
The total station functions by emitting a laser beam toward a reflective target placed on the bridge. The time it takes for the laser to travel to the target and return to the station is used to calculate the distance. By measuring angles and distances from the instrument to the target,
the total station can determine the target’s X, Y, and Z coordinates, allowing engineers to track movements in real time with millimeter precision.
5.2. Total Station Setup for Bridge Load Testing
Instrument Placement
The total station is set up at a fixed location, typically some distance from the bridge. The position of the instrument is carefully calibrated to ensure that it can measure the movements of reflective targets accurately. The setup involves:
- Establishing control pointson the bridge that are used for reference.
- Mounting the instrument in a stable position with an unobstructed line of sight to the bridge.
Target Installation
Reflective prisms or targets are placed on specific parts of the bridge where movement or deflection is expected. These targets are affixed securely to the bridge using mounting brackets, ensuring their position remains fixed throughout the test. The targets should be placed at:
- Critical pointswhere deflection is expected to be highest, such as mid-span, near supports, or critical joints.
- Even distributionacross the structure for a complete view of bridge behavior.
5.3. Measurement During Load Testing
As the test vehicles or loads are applied, the total station continuously measures the displacement of the targets. Unlike dial gauges, the total station can measure movements in three dimensions (X, Y, Z) and can track both vertical and horizontal displacements.
- The vertical displacementhelps assess how much the bridge sags or deflects under load.
- The horizontal displacementprovides information about lateral movement or shifts, which can indicate how the structure responds to uneven loading or forces.
5.4. Advantages of Total Station Testing
- High Precision: Total stations can measure movements with sub-millimeter precision, ensuring highly accurate data collection.
- Non-Contact Measurement: Since the total station measures displacement remotely via laser, it does not require contact with the bridge, making it ideal for measuring hard-to-reach or sensitive areas.
- Real-Time Data Collection: Engineers receive real-time measurements, which allows for immediate data analysis and adjustments during the testing phase.
- Comprehensive Coverage: Multiple targets can be measured simultaneously, providing a more holistic view of the bridge’s behavior under load.
5.5. Limitations of Total Station Testing
- Line of Sight: The total station requires an unobstructed line of sightbetween the instrument and the reflective targets, which may be difficult to maintain if there are large structures or traffic between the instrument and the bridge.
- Setup Complexity: Setting up a total station requires careful calibration and precise placement of both the instrument and the targets. Skilled technicians are often required for this task.
- Cost: Total stations can be relatively expensive, making them less cost-effective for small-scale testing or where only limited data is required.
- Benefits of Bridge Load Testing
Through the use of tools like dial gauges and total stations, engineers can conduct thorough bridge load testing that provides a wealth of information, leading to numerous benefits, including:
- Safety Assurance: Testing helps ensure that bridges are safe to use, preventing accidents caused by unexpected failures or weak points in the structure.
- Informed Structural Decisions: Data gathered from the load test enables engineers to make informed decisions on maintenance, rehabilitation, or replacement.
- Cost-Efficiency: Identifying potential structural problems early through load testing allows for targeted repairsrather than costly emergency interventions.
- Conclusion
Incorporating tools such as dial gauges and total stations into bridge load testing allows for highly accurate and detailed assessments of the bridge’s deflection and overall behavior under load. These methods provide engineers with precise data that can inform maintenance, safety assessments, and long-term planning for infrastructure management. By conducting thorough load testing, bridge operators can ensure the safety and reliability of these critical structures, safeguarding both public and operational interests.
- Duration of Bridge Load Testing
The duration of bridge load testing can vary depending on several factors, including the complexity of the bridge structure, the types of tests being performed, and the specific tools used. Here’s a breakdown of how long each phase might take and the factors that influence the total testing period:
8.1. Factors Affecting Duration
Several factors influence how many days a bridge load test will take. These include:
- Size and Complexity of the Bridge: Larger and more complex bridges (such as multi-span or suspension bridges) typically require more time to test due to their size, number of structural components, and the variety of load positions tested.
- Type of Load Testing: The type of load testing being performed also influences the time required. Static load testing(where loads are applied and monitored at specific points) may take longer than dynamic testing (where moving loads are used to simulate real-world conditions).
- Number of Measurement Points: The number of measurement points where dial gaugesor reflective targets are placed can add time to the setup and testing phase. More measurement points provide more detailed data, but also require more installation time and data collection.
- Testing Equipment: The use of sophisticated instruments such as total stationsand the associated setup time for calibration and alignment can also affect how long the test takes. For example, a total station setup requires careful calibration to ensure accurate measurements across multiple targets.
- Weather and Environmental Conditions: Adverse weather (rain, snow, high winds) may delay or interrupt testing. While testing equipment like total stations and dial gauges are generally resilient, poor weather conditions can affect worker safety and logistical processes.
- Traffic Control: If the bridge is in use by vehicular traffic, it may be necessary to block lanes or completely close the bridge for safety. Coordination with local authorities to manage traffic or reroute it can also add time to the process.
8.2. Typical Duration of Testing
Here’s a general breakdown of the time required for different stages of the testing:
- Pre-Test Preparation:
- Duration: 1 to 2 days.
- Activities: Initial surveys, site assessments, equipment setup, and planning. During this phase, engineers will inspect the bridge, identify measurement points, install preliminary equipment (such as reflective targets or baseline dial gauges), and calibrate instruments (especially total stations).
- Setup and Instrumentation:
- Duration: 1 to 2 days.
- Activities: The setup phase can take up to 2 daysdepending on the complexity of the bridge and the number of measurement points. During this time, the dial gauges and total stations (or other instruments like strain gauges) are mounted at strategic locations on the bridge. Multiple reflective targets are typically positioned, and equipment calibration is performed.
- Static Load Testing:
- Duration: 1 to 2 days.
- Activities: Static load testing involves applying heavy loads to the bridge (usually by positioning trucks or other load-bearing equipment) in incremental steps. Data collection occurs throughout this phase, with engineers measuring deflectionsand displacements at multiple points on the bridge. This phase typically lasts for 1 to 2 days, depending on the complexity of load application and the number of measurement points.
- Dynamic Load Testing (if applicable):
- Duration: 1 to 2 days.
Activities: If dynamic load testing is part of the plan (simulating moving traffic), this can take an additional 1 to 2 days. The total station or other measuring equipment will track the displacement of targets as moving vehicles
- cross the bridge. This phase tests how the bridge behaves under real-world, dynamic conditions. It often requires several runs to ensure comprehensive data collection, which can extend the testing period.
- Post-Test Data Analysis and Reporting:
- Duration: 1 to 3 days.
- Activities: After the data is collected, engineers analyze the results to evaluate the deflection, displacement, and overall behavior of the bridge. This analysis may require several days to ensure accuracy. If there is a need to perform additional calculations or run simulations based on the data, this phase could take longer. Final reports, recommendations for repairs, or validation of design assumptions will also be created.
8.3. Total Time for Bridge Load Testing
- For smaller bridges or simpler tests, the total duration of bridge load testingcould take 3 to 5 days. This includes setup, testing, and initial analysis.
- For more complex bridges or if multiple tests (e.g., static and dynamic testing) are involved, the process can take up to 7 to 10 days.
8.4. Breakdown of Time for a Typical Bridge Load Test
- Day 1: Pre-test preparation and site survey.
- Day 2: Equipment setup, calibration of total stations and dial gauges.
- Day 3: Static load testing and initial data collection.
- Day 4: Static load testing continues, more measurements are taken.
- Day 5: Dynamic load testing (if applicable) and data collection.
- Day 6: Post-test data analysis, including reviewing deflections and displacement data.
- Day 7-8: Report generation and recommendations.
- Conclusion on Duration
The duration of a bridge load test can vary based on multiple factors, but for a typical test using both dial gauges and total stations, it generally takes between 3 to 7 days. The complexity of the test, size of the bridge, weather conditions, and the specific goals of the testing program all contribute to the time required to complete the entire process. Proper planning, equipment calibration, and efficient data collection and analysis can help ensure that the test is completed within a reasonable timeframe, providing engineers with the crucial data they need to evaluate the safety and integrity of the bridge.
- cross the bridge. This phase tests how the bridge behaves under real-world, dynamic conditions. It often requires several runs to ensure comprehensive data collection, which can extend the testing period.